What is Cat® Dynamic Gas Blending™ and what are the benefits?
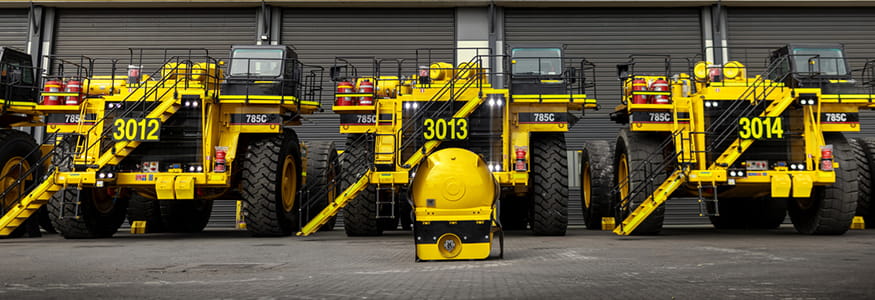
While the end game for many miners is total elimination of fossil fuels from their operations, several pieces of the puzzle are yet to fall into place before options such as battery or hydrogen power become viable for haulage fleets.
The diesel-and gas-powered reciprocating engine still presents a strong economic value proposition for most mining operations and its environmental value continues to improve with advancements in emissions reduction technology and the availability of cleaner burning fuels such as Liquified Natural Gas (LNG).
Caterpillar’s new Dynamic Gas Blending (DGB) system is a sensible step towards reducing exhaust emissions and has been introduced to help mining operations achieve greater sustainability and value in their operations.
As the name suggests, the DGB system dynamically utilises a combination of gas and diesel, automatically maximising LNG usage to displace diesel without impacting performance. By reducing overall diesel consumption, the system allows operators to reduce fuel spend and extend asset life.
The system can be fitted in the factory to new equipment or provided as a conversion kit for existing mining trucks. That includes dual fuel tanks which fit into the same footprint as a standard diesel tank, engine and chassis conversion kits, and the software required to control and optimise fuel delivery. Rebuilding an existing mining truck presents a perfect opportunity to utilise the conversion kit.
According to WesTrac NSW Mining Business Manager Gary Rayner, the DGB system is currently supported in larger haul trucks including the 785C and 793D Cat mining trucks.
“It's estimated that customers who use this technology will save considerably on fuel costs using DGB compared to straight diesel,” Gary said.
“The other benefit is that to convert to DGB, you don't actually have to remove the engine or open it up to the elements. You can install the product while the engine is still in the truck.”
To learn more about DGB technology, watch the explainer video below.
According to WesTrac WA Account Manager Mining Paul Niven, DGB is well suited to remote operations in regions where diesel quality may fluctuate.
“LNG is consistent wherever it is, but in areas where there could be issues with diesel quality and contamination, the DGB system could be very beneficial,” Paul said.
“By blending LNG with diesel, there’s a higher-octane content so it burns a lot cleaner, cleans and protects the engine and therefore means lower exhaust emissions and better efficiency.”
There are obviously infrastructure requirements including a reliable supply of LNG, and storage and refueling facilities, as well as the training requirements to ensure safe handling of the gas.
While operators will ideally be able to realise a return on their DGB investment immediately, there are options to run wholly on diesel even after conversion.
If that is likely to be for an extended period – for example while a site is waiting for infrastructure to be installed – the dual tanks can temporarily be replaced with a standard diesel tank then swapped out when the site is equipped to take full advantage of its DGB system.
For a mining operation adopting this technology now, that could provide the flexibility to deploy its haul fleet to any site and move trucks between sites with the relatively simple change of a fuel tank.
Watch the video below to discover what the DGB system did for a gold mine in Mexico.
Caterpillar has collated more than 10 million hours of live operational data from mine sites around the world that have been operating DGB systems for several years.
Key statistics gathered from sites using DGB as far afield as the USA, Mexico and Turkey include:
If you want to find out more about Dynamic Gas Blending, contact us today.